Omni Hotel
Jacksonville, FL
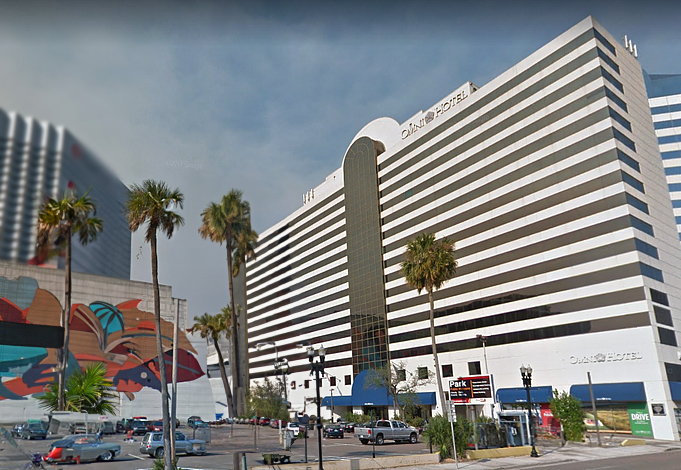
ThermaServe Delivers Seamless Chiller Plant Upgrade in Record Time, Slashing Energy Costs Dramatically.
The Omni Hotel in Jacksonville, Florida, needed to replace their aging penthouse chiller plant equipment, all while the hotel remained occupied. ThermaServe was able to complete a five-day install in only 16 hours—and provide energy savings of nearly a third of the annual cost per operating year.
Challenge
The Omni Hotel in Jacksonville, Florida, a four-diamond, 16-floor luxury hotel, was built in the late 1980s. The Omni’s original 26-year-old penthouse chiller plant needed to be replaced with more efficient equipment, and the chillers contained CFC ozone-depleting refrigerant and were very loud, hindering the rental of penthouse suites.
Analysis
Based on the survey and analysis performed by ThermaServe, we were able to specify the equipment necessary to replace the existing equipment for an energy-saving modernization. This included variable speed drives incorporated with a new cooling tower and new secondary chilled water pumps, along with two new quieter variable speed drive chillers.
Solution
Our solution was to provide two 500-ton variable-speed centrifugal chillers with ozone-friendly refrigerant. Next, we replaced the existing three cooling towers with one new three-cell stainless steel cooling tower with a greatly improved physical footprint and added six new pumps with variable-speed drive motors for efficient operation. The mechanical modernization also included new butterfly valves and piping reconfiguration for the new equipment. The solution also included connecting all the new equipment to the Delta Controls DDC building automation system with a condenser water outdoor wet bulb reset control program for optimized cooling tower fan operation.
Scope of Services
The chiller plant replacement was undertaken with an occupied and running hotel. The majority of the work was performed during the cooler months of the year to reduce the impact on the hotel, and further preparation and smaller equipment replacements were performed before the week of demolition and heavy equipment crane lifting. We disassembled and removed the existing cooling tower system and one chiller, installed, and brought a new chiller on-line, then disassembled and removed the other chiller and still kept the hotel running. The cooling tower replacement was the critical element to maintaining cooling for the entire new system cut over. We allotted 24 hours of full downtime for the hotel for the cooling tower installation and only took a remarkable 16 hours to complete a five day install.
Results
In addition to greatly improved guest comfort, the projected chiller plant energy savings are 29% or nearly a third of the annual cost per operating year. This is in addition to the (one-time) JEA utility rebate projecting a less than 10-year payback for this nearly $1M chiller plant modernization project.
← Return to Projects